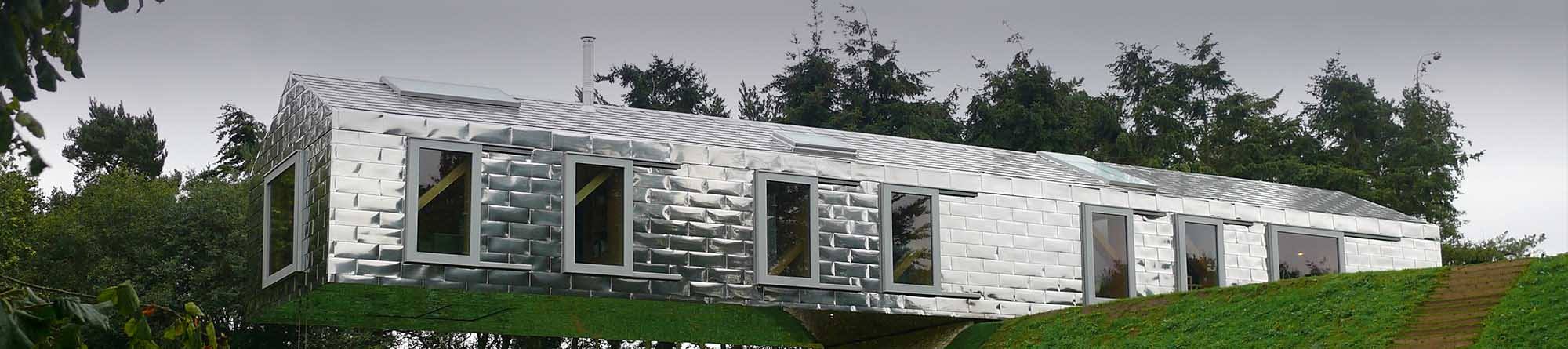
Home Projects
Projects
Take a look at the many projects that have benefited from stainless steel.
Our portfolio includes everything from the latest trends in everyday buildings to some of the world’s most aesthetically daring designs.
Paul Klee Center
The steel ribs, clad with stainless steel, blend in with the patterns found in the surrounding fields.
Located on the outskirts of the city of Bern, the Zentrum Paul Klee, with the Alps as background, is articulated around three artificial hills: the central hill containing the exhibition section, the north hill housing a multifunctional room, an auditorium and a children´s museum, and the south hill, a space reserved for research and management activities.
The majority of the works that form the museum´s collection cannot be exhibited for reasons of preservation but they will be made available to researchers. To ensure the optimum preservation conditions, this museum will not benefit from zenital light, but it will be illuminated from the west façade, through which light will be filtered by a system of translucent screens, creating softer light.
Elevated on the land slope, the three hills are mutually chained like three waves, their undulation decreasing with the building elevation and their span being partially below the ground level. These wave-like spaces are interconnected by a covered passageway. The undulation is transposed in a continuous way from one end of the building to the other under a roof that is clad using Uginox Top, a matt-finished stainless steel product. Taking into consideration the roof´s geometry, 0.4 mm-thick stainless steel sheets have been modelled in the mill before been installed on a wood structure.
The structure, which intentionally remains visible both from the inside and from the outside, is formed by a series of parallel steel arches, whose pieces, produced by means of CNC equipment, have been manually welded. Steel was found to be only material to provide an adequate response to the largely different stresses, as it allows variations in the plate thicknesses without changing material sections.
High variations exist in the arches´ height/span ratio, depending on the point considered in each case. The reinforced concrete support points allow standing horizontal forces in collaboration with the floor slabs. Two series of tie rods guarantee the cross-sectional stability of the arches: in their top arch section, 48 mm-section tubes are used to support the lattice elements, whereas in the bottom section HEB 140 are employed. The thermal insulating material has been placed under the tubes so that these remain visible.
Façades absorb any roof deformation caused by exploitation loads and temperature variations. A 6.5 m-span overhang, fabricated with HEB160, is suspended from the roof by cables and is supported on the stanchions of the bottom section of the façade, i.e., two flat-rolled steel plates.
Stainless steel advantages:
- A suitable aspect for this type of contemporary architecture
- A low thermal expansion coefficient allows the installation of continuous sheet lengths up to 20 m
- Easy implemantation allowing a perfect fit of the curvature of the roof
- High mechanical properties for an equivalent resistance to a given effort, allowing the use of small thickness (0.4 mm in this case).
Technical Files
Info
Saint-Lawrence Church
“The roof needed to be renewed following a severe single incidence of Lead theft where 50% of the Lead across the east end of the church was stolen in one night. The parish were not insured for such a large amount of metal theft and they decided to be pro-active and remove what was left. The dull grey characteristics of the UGINOX Patina and its ability to be laid on batten rolls at spacing centres that replicated Lead were factors that persuaded the local authorities and English Heritage the change of material was acceptable.“ Andrew Wiles, Wiles and Maguire Ltd.
Uginox Patina offers durability thanks to the robust stainless steel composition that completely fits with the Doncaster environment which is classified as a mildly marine atmosphere. Local weather conditions have enhanced the dull grey patina growth over only a few months. The Tin oxides forming on the stainless steel surface means the material evolves when it is installed on site. Its traditional appearance blends perfectly within heritage sites such as here on St Lawrence Church.
Uginox Patina was installed using a welted batten roll in order to give a resemblance of the detail of the original roof.
Uginox Patina properties give the roof excellent resistance during bad weather and high wind loading. Moreover its exceptional mechanical features offer a flat aspect with only a 0.5 mm gauge lightweight stainless steel.
Uginox Patina is known as a very sustainable material and the electro-tinned coating is lead-free providing an inert material regards the environment.
Uginox Patina doesn’t leach harmful compounds that could interfere with rainwater.
Technical Files
Info
Mirror of movement
The Philharmonie de Paris, designed by Ateliers Jean Nouvel, is a glittering hill culminating at 52 meters with a giant screen displaying its programme, an eye-catching feature visible from the Périphérique and surrounding suburbs. Its location to the north-east of the capital , in the heart of the metropolis,made it a landmark of Greater Paris from the outset and affirmed a desire to popularize the music it represents. It marks the culmination of the cultural metamorphosis of this sector in the 19th arrondissement that was formerly dedicated to slaughterhouses – the transformed Grande Halle bears witness to this – that started over 30 years ago. With its national and international dimension, the Philharmonie crowns all the facilities that dot Parc de La Villette, and in particular its opposite number Cité de la Musique, completed in 1995 by the architect Christian de Portzamparc. These two buildings now form a pair known as Philharmonie 1 and 2.
In addition to the large philharmonic hall named after Pierre Boulez with 2400 seats (3600 standing) set out over five levels, the Philharmonie comprises two large orchestra rehearsal rooms, six rehearsal rooms, work studios, an administrative centre, an educational centre, exhibition spaces, catering areas and shops. Concerts as well as exhibitions, educational activities and residences bring life to the building. There are several different ways of entering the building. Firstly, you can go ‘under’ the building from Parc de La Villette on the ground floor level. Alternatively, you can climb a very wide staircase that brings you into the foyer of the great hall. A gentle ramp from Porte de Pantin also leads to this foyer. You can zigzag up the northern slope of the building, like a hillside, to reach the belvedere, 37 meters above the ground, that offers a panoramic viewpoint of the city, The various paths offer freedom to users, inviting them to appropriate the site without preconceptions. A “living space for music”, its singular plasticity reflects the fluidity sought between spaces and people be they artists, technicians, the public, or merely shoppers.
Mirror of movement
Outside, the metallic cladding of its angular shapes and, conversely, curves provides a distorted reflection of the landscape and the movements around it, confusing distance and scale. Elements collide. The main design of the façades, in a nod to M.C. Escher, assembles seven different models of a stylised bird to form the aluminium coating in four shades of matt grey: flocks of birds form as the light changes.
Tourbillon
Overflowing from these flat, sharpedged façades, the heart of the building is covered with bright stainless steel plate (Uginox Bright). Called the Tourbillon (whirlpool) and developed by Bureau HDA, this volume, highlighted in this manner, seems to escape from inside. It corresponds to the spaces of the foyer of the great hall. This curved wall is built in such a way as to form two distinct skins – the outer cladding and a watertight inner wall – each defined according to distinct geometric principles. The space between the two allows access for maintenance. With a surface area of nearly 7000m², the cladding is a collection of stainless steel scales laid out in a freeform manner determined by the architects. The geometry follows a NURBS (Non- uniform rational B-spline) model. It is characterized by a mixture of zones of double convex, concave and, in some places, almost flat curves. With a thickness of 1.5 mm, the stainless steel sheets are fixed on a three-dimensional structural system combining flat sheets for the frames and curved tubes. These are connected to the edges of the floor with rods.
In contrast to the matt outer layer, the shiny appearance of the stainless steel exaggerates the surrounding landscape. Besides its aesthetic appearance, the smoothness of its surface helps to limit the deposition of dust and pollution residues. The particularly aggressive atmosphere near the Périphérique justified the choice of grade of austenitic stainless steel (Aperam 316L).
Technical Files
Info
Arc Iris centre de tri
“Any architect can make a beautiful industrial object. But the important thing is that the envelope provides an emotion. ” A masterpiece open-air shimmering in all its facets, Caiman imposes itself as a monumental sculpture. Its scales reflect the light, the sky and the earth according to the hours and the seasons. Dressed in natural colors, the building becomes alive, blends into the environment, participates in the landscape in its diurnal and nocturnal evolution. This metal envelope reflects a single architectural quest: that of contemplation. Household waste incineration plants may have been renamed the less worrying name of “energy recovery center”, they arouse oppositions of residents increasingly frequent. To better accept them, their architectural quality appears as an asset. Because there is a risk of real blockage linked to the syndrome NIMBY (“not in my back yard”), come from overseas and now well established in France. Or how waste treatment should always be done elsewhere, far from home … This is a phenomenon that had to be confronted to achieve in Calce, near Perpignan, an energy recovery center of 22 tons / hour. Winners of a design competition with Cydel (TIRU Group), the architects Luc Arsène-Henry Jr and Alain Triaud proposed to bring to the front of the undulating facades of their building project a coat of metal bands with more fluid lines. . “The plant must be beautiful because it is proof that the company looks after you. It is no longer necessary that it expresses the industrial vocation because technicality is now a due: a sports car does not show its engine, but its curves. ” Leaning against the rock, the new center stretches over 1500 m long, between evocation of vestiges and great artistic gesture. The champagne anodized stainless steel that was finally chosen helps to melt the building in the ocher land of the scrubland, thus contributing to a better acceptance of its location. In order to recall the local geology, the site has also been developed with the implementation of architectural embankments and a base of raw concrete. Plantations did the rest. With 10,000 m² of cladding laid, the implementation of colored stainless steel represents a first by the scale. The coloring of the sheet, of a thickness of 0.5 mm, was carried out by bath, in an electrolytic process. The subcontractor who shaped the tiles has developed with the architect the necessary one hundred modules with an average size of 950 x 600 mm. This execution was made in the factory so as to avoid the risk of deformation. On the site, a modular galvanized steel support made it possible to fix this kit of precision before mounting the assembly on the secondary framework of the facade. The scales are laid over without visible screws, in a direction that leaves no wind. To point out already the south-east / north-west orientation of the building, chosen according to the winds to minimize its sound impact. The cost of this dressing is compensated by the reduction of the center footprint area, obtained by a studied spatialization of the process. The arrangement of the latter in the slope prevents the plant that hides it from exceeding the ridge line. Even the emergence of the chimney has been reduced to 3 m above the frame, so as not to remind residents of the idea of pollution to which this industrial element refers.
Technical Files
Info
Need
inspiration?
Take a look at the many projects that have benefited from stainless steel.
Our portfolio includes everything from the latest trends in everyday buildings to some of the world’s most aesthetically daring designs.
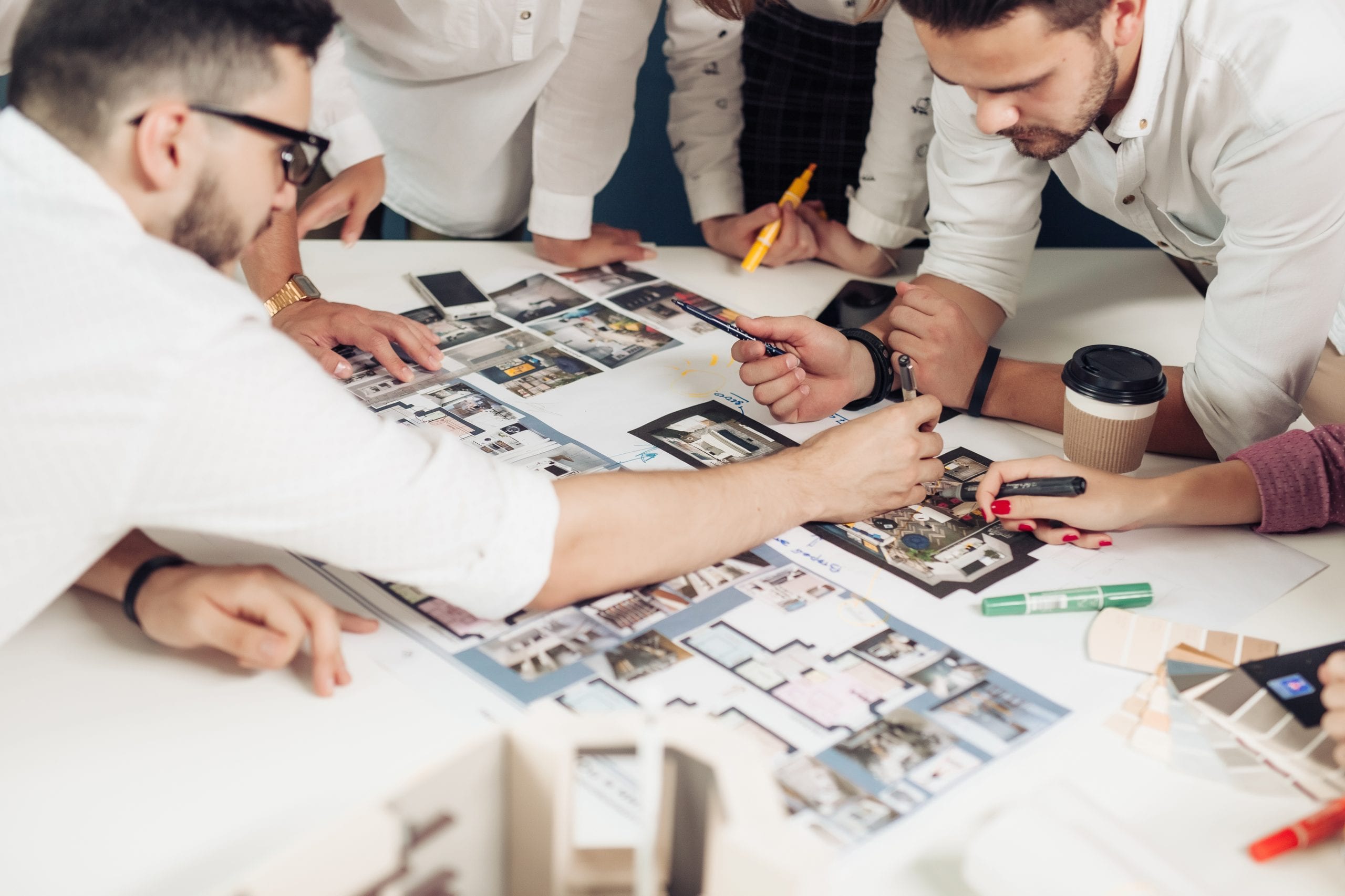
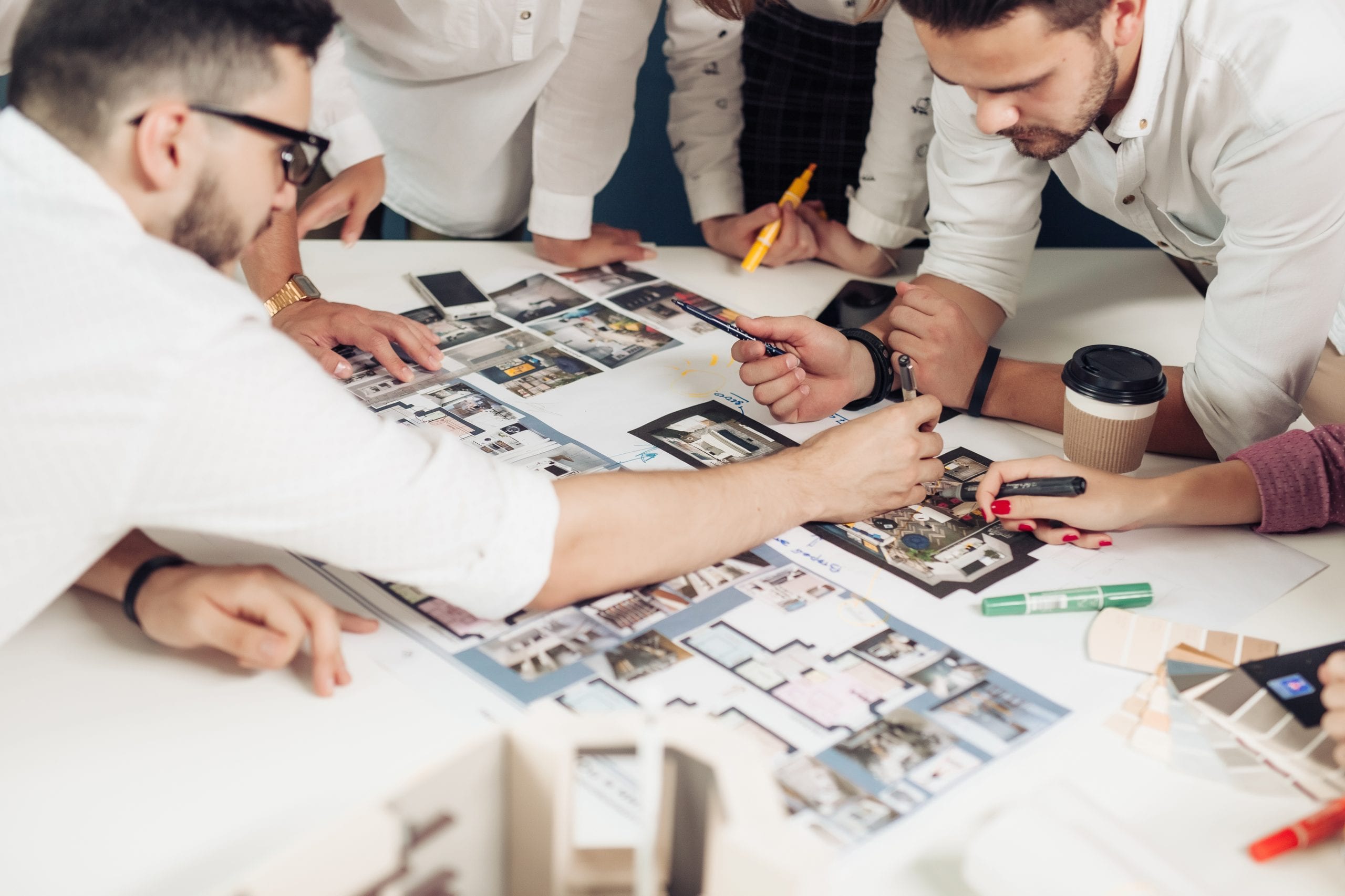
Sign up for the Newsletter
Whether you’re an architect, an installer or a design firm, keep up to date with the latest Uginox news by subscribing to our Newsletter.
Consult our Privacy and Cookies Policy.